King® MS-D3
King® MS-D3 is a high early strength, preblended, and pre-packaged shotcrete material formulated for dry-mix process applications. It contains high early Portland cement, silica fume, air-entraining admixture, blended aggregates, along with other carefully selected components. It has greatly enhanced shooting characteristics and physical properties, along with high early strength development.
- Improved early age strength development
- Air-entrainment provides superior resistance to freeze-thaw cycling and salt-scaling resistance
- Improved adhesive and cohesive plastic properties
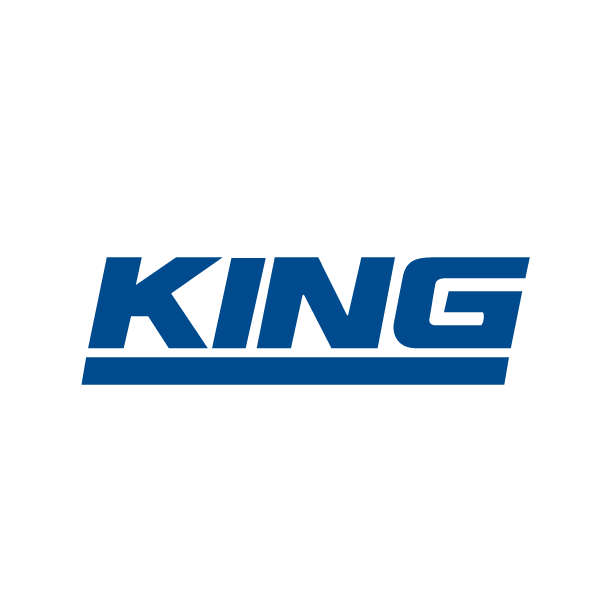
Usage
Overall:- Rehabilitation of concrete bridges, dams, reservoirs, tunnels, marine structures, and parking ramps
- Lining and rehabilitation of sewers and watermains
- New construction including slope stabilization, soil-nailing, shaft and tunnel linings, pools and other concrete structures
- Ground support applications for mining, tunneling, and other underground openings
- Rehabilitation of marine structures
- Lining and rehabilitation of sewers and other tunnels
- Slope stabilization, soil-nailing, shaft and tunnel linings
Advantages
- Improved early age strength development
- Air-entrainment provides superior resistance to freeze-thaw cycling and salt-scaling resistance
- Improved adhesive and cohesive plastic properties
- Significantly reduced rebound, resulting in lower material usage
- Improved ability to build greater thicknesses in a single pass in both vertical and overhead orientations
- Improved resistance to water wash-out
- Improved resistance to sulphate attack
- Very low permeability
- Low shrinkage
- Compatible with integral, pre-applied and/or post-applied corrosion inhibitors
- Designed with natural normal-density non-reactive aggregates to eliminate potential alkali-aggregate reactivity (AAR)
Accelerator Level
- Improved performance in cold temperatures
- Improved performance in presence of running water
- Allows for earlier re-opening of traffic lanes on bridges and in subway tunnels
- Micro-Synthetic fibers reduce cracking caused by intrinsic stresses
- Type III synthetic fiber in accordance with ASTM C1116
- Grade FR Class I shotcrete in accordance with ASTM C1480
- Improved performance in cold temperatures
- Improved performance in presence of running water
- Air-entrainment provides superior resistance to freeze-thaw cycling and salt-scaling resistance
- Significantly increased load carrying capacity
- Significantly increased energy absorbing capacity (toughness)
- Significantly increased impact resistance
- Improved adhesive and cohesive plastic properties
- Improved resistance to water wash-out
- Low permeability
- Reduction of cracking due to drying shrinkage
- Corrosion inhibitor protects steel reinforcing and other metals embedded in concrete from corrosion induced by carbonation or chlorides
- Pre-blended corrosion inhibitor provides the correct dosage to enhance corrosion protection
- By default King® MS-D3, King® MS-D3 MF, and King® MS-D3 ST are blended to meet ACI 506 “Guide to Shotcrete”, Table 1.1, Gradation No. 1 (No Added Abbreviation)
- King® MS-D3 G2, King® MS-D3 ST G2, and King® MS-D3 MF G2 are blended to meet ACI 506 “Guide to Shotcrete”, Table1.1, Gradation No. 2 (G2)
- Improved performance in cold temperatures
- Improved performance in presence of running water
- Significantly decreased wear on placing equipment and accessories when compared with steel fibers
- Increased fire resistance
- Ideal for use in manways or other areas where people may come in contact with the shotcrete surface
- Significantly increased load carrying capacity
- Significantly increased energy absorbing capacity (toughness)
- Significantly increased impact resistance
- Low permeability
- Reduction of cracking due to drying shrinkage
- For King® MS-D3 with a level 3 dosage of accelerator, with micro-synthetic fibers and gradation No. 2, the name of the product would be:
King® MS-D3 X3 SY G2. - For King® MS-D3 ST with a high dosage of steel fiber, a level 2 dosage of accelerator and a gradation No. 1, the name of the product would be:
King® MS-D3 X2 STA. - For King® MS-D3 MF with a level 2 dosage of accelerator, a high dosage of macro-synthetic fiber and gradation No. 1, the name of the product would be:
King® MS-D3 X2 MFB.
Packaging
66 lb (30 kg) bag
2205 lb (1000 kg) FIBC*
Products with Macro-Synthetic fibers (MF) or Steel fibers (ST) can only be packaged in FIBC*
Custom packaging is available to suit specific project requirements
*Flexible Intermediate Bulk Container
Product Details
Shelf Life
12 months in original, unopened packaging
Storage Conditions
Store in a dry, covered area, protected from the elements between
40°F - 95°F (5°C - 35°C)
Underground Environments
Physical properties may be adversely affected if material is stored in temperatures below 40°F (5°C) and should be allowed to warm to ambient underground temperatures before application
Compressive Strength
ASTM C116 (MODIFIED) |
King® MS-D3 X | King® MS-D3 X2 | King® MS-D3 X3 | |
4 Hours | - | 290 psi (2 MPa) | 1015 psi (7 MPa) |
8 Hours | 1015 psi (7 MPa) | 1150 psi (8 MPa) | 1500 psi (10 MPa) |
12 Hours | 1500 psi (10 MPa) | 1750 psi (12 MPa) | 2030 psi (14 MPa) |
ASTM C1604 |
King® MS-D3 | King® MS-D3 X | King® MS-D3 X2 | King® MS-D3 X3 | |
1 Day | 3000 psi (21 MPa) | 3625 psi (25 MPa) | 3625 psi (25 MPa) | 3625 psi (25 MPa) |
3 Day | 4350 psi (30 MPa) | 4350 psi (30 MPa) | 4350 psi (30 MPa) | 4350 psi (30 MPa) |
7 Day | 5075 psi (35 MPa) | 5075 psi (35 MPa) | 5075 psi (35 MPa) | 5075 psi (35 MPa) |
28 Day | 6000 psi (42 MPa) | 6000 psi (42 MPa) | 6000 psi (42 MPa) | 6000 psi (42 MPa) |
Modulus of Elasticity in Compression
ASTM C469 |
1 Day | 3.0 x 106 psi (20.8 GPa) |
7 Days | 3.2 x 106 psi (22.0 GPa) |
28 Days | 3.7 x 106 psi (25.4 GPa) |
Flexural Strength
ASTM C78 |
King® MS-D3 | King® MS-D3 X | King® MS-D3 x2 | King® MS-D3 X3 | |
7 days | 940 psi (6.5 MPa) | 870 psi (6.0 MPa) | 870 psi (6.0 MPa) | 870 psi (6.0 MPa) |
28 days | 1085 psi (7.5 MPa) | 1015 psi (7.0 MPa) | 1015 psi (7.0 MPa) | 1015 psi (7.0 MPa) |
King® MS-D3 ST & King® MS-D3 MF | ASTM C78 |
28 days | 1160 psi (8.0 MPa) |
Tensile Strength
TENSILE BOND STRENGTH | ASTM C1583 |
7 Days | 320 psi (2.2 MPa) |
28 Days | 335 psi (2.3 MPa) |
Splitting tensile strength
ASTM C496 |
7 Day | 640 psi (4.4 MPa) |
28 Day | 65 psi (4.6 MPa) |
Slant Shear Strength
7 Days | 3060 psi (21.0 MPa) |
28 Days | 3625 psi (25.0 MPa) |
Shrinkage
King® MS-D3 | King® MS-D3 X | King® MS-D3 X2 | King® MS-D3 X3 | |
28 Days | 0.050 % | 0.060 % | 0.060 % | 0.060 % |
56 Days | 0.058 % | 0.065 % | 0.065 % | 0.065 % |
Coefficient of Thermal Expansion
CRD-C39 |
28 Days | 4.5 x 10-6/ ºF (8.1 x 10-6/ ºC) |
Porosity
AIR CONTENT
6% ± 2% | ASTM C457 |
MAXIMUM AIR VOID SPACING FACTOR
0.0118 in (300 µm) | ASTM C457 |
BOILED ABSORPTION
6.0% | ASTM C642 |
MAXIMUM VOLUME OF PERMEABILITY VOIDS
15.0% | ASTM C642 |
Freeze-Thaw Stability
|
Salt resistance
King® MS-D3 | King® MS-D3 X | King® MS-D3 X2 | King® MS-D3 X3 |
0.02 lb/ft2 (0.10 kg/m2) | 0.035 lb/ft2 (0.17 kg/m2) | 0.04 lb/ft2 (0.20 kg/m2) | 0.24 lb/ft2 (1.2 kg/m2) |
Application
Set Time
ASTM C1117 |
King® MS-D3 | King® MS-D3 X | King® MS-D3 X2 | King® MS-D3 X3 | |
Initial | 3 hours | 45 minutes | 15 minutes | 3 minutes |
Final | 5 hours | 60 minutes | 25 minutes | 5 minutes |
Coverage
Approx. 0.5 ft3 per 66 lb bag (0.014 m3 per 30 kg bag)
Approx. 16.5 ft3 per 2205 lb FIBC (0.45 m3 per 1000 kg FIBC)
*May vary according to projects conditions
EQUIPMENT
Special precautions needed when using predampeners with dry blended powdered accelerated shotcrete.
Contact your Sika STM Technical Representative in for more information.
SURFACE PREPARATION
Temperatures above 40 °F (5 °C):
- Repair or Rehabilitation : All surfaces to be in contact with King® MS-D3 and its variations must be free from dust, oil, grease or any other foreign substances that may interfere with the bond of the material. Remove all loose or delaminated concrete providing a roughened surface and a minimum of 20 mm (¾ inch) clearance behind any corroded reinforcing steel. The perimeter of the repair area should be sawcut a minimum of 20 mm (¾ inch). Clean the area to be repaired with potable water, leaving the concrete saturated but free of standing water (SSD).
- Rock Surfaces : All surfaces to be in contact with King® MS-D3 and its variations must be free from dust, oil, grease or any other foreign substances that may interfere with the bond of the material. Remove all loose or delaminated rock. Clean the area with potable water, leaving the substrate saturated but free of standing water (SSD).
Temperatures below 40 °F (5 °C):
Use King® MS-D3 (X2 / X2 MF / X2 ST)
or King® MS-D3 (X3 / X3 MF / X3 ST)
- Repair or Rehabilitation: All surfaces to be in contact with King® MS-D3 X2 or King® MS-D3 X3 must be free from oil, grease or any other foreign substances that may interfere with the bond of the material. Remove all loose or delaminated concrete providing a roughened surface and a minimum of 1 inch (25 mm) clearance behind the reinforcing steel. The perimeter of the repair area should be sawcut a minimum of ¾ inch (20 mm). To avoid freezing of the interface between the shotcrete and the parent concrete, do not pre-wet the receiving surface. Pneumatically remove any free standing or other fine particles that may interfere with the bond between King® MS-D3 X2 or King® MS-D3 X3 and the substrate. Do not apply King® MS-D3 X2 or King® MS-D3 X3 when ambient temperature is below or is expected to fall below 20 °F (–5 °C) within 6 hours following the application of shotcrete. Do not apply when temperature of receiving surface is below 20 °F (–5 °C). Material temperature should be maintained above 50 °F (10 °C) at the time of application. Mixing water temperature should be maintained between 70° F (20°C) and 80 °F (25 °C).
- Rock Surfaces: All surfaces to be in contact with King® MS-D3 X2 or King® MS-D3 X3 must be free from dust, oil, grease or any other foreign substances that may interfere with the bond of the material. Remove all loose or delaminated rock. To avoid freezing of the interface between the shotcrete and the parent concrete, do not pre-wet the receiving surface. Pneumatically remove any free standing or other fine particles that may interfere with the bond between King® MS-D3 X2 or King® MS-D3 X3 and the substrate.
APPLICATION
Apply in accordance with the ACI 506 “Guide to Shotcrete” publication.
Performance of in-place shotcrete relies heavily upon application techniques. The shotcrete material, equipment and key personnel should be pre-qualified prior to project start-up to ensure optimum quality of in-place shotcrete
OPTIMUM PERFORMANCE
- King® MS-D3, King® MS-D3 X, King® MS-D3 MF, King® MS-D3 X MF, King® MS-D3 ST, and King® MS-D3 X ST should not be applied when ambient, substrate, and material temperatures are below 40 °F (5 °C) or above 95 °F (35 °C).
- King® MS-D3 X2 and King® MS-D3 X3 should not be applied when ambient and substrate temperatures are below 20 °F (-5 °C) or when ambient, substrate and material temperatures are above 95 °F (35 °C).
- For adverse temperatures, follow ACI recommendations for Cold / Hot Weather Concreting.
- When using King® MS-D3 MF or King® MS-D3 ST, recommened minimum inside diameter of shotcrete hoses should be 2 inch (50 mm).
Contact your Sika STM a Technical Representative for more information.
CURING TREATMENT
Curing is essential to optimize physical properties of the shotcrete and minimize plastic shrinkage. Product should be cured immediately after material has reached initial set in accordance with ACI 308 “Guide to Curing Concrete”. Continuously moist cure for a minimum period of 7 days. Alternatively, moist cure for a minimum period of 24 hours and apply a curing compound that complies with ASTM C 309. Curing is particularly critical in rapid moisture loss conditions such as high temperatures, high winds and low humidity.
Underground environments
Good curing conditions are beneficial to optimizing physical properties. Although the high relative humidity commonly found in underground environments provides for good curing conditions, additional curing is often appropriate and should be performed in accordance with ACI 308 “Guide to Curing Concrete''.
For temperatures below 40 ºF (5 °C):
A resin based liquid membrane curing compound approved for use in cold weather conditions should be applied immediately after shotcrete
reaches final set be applied immediately after shotcrete reaches final set.
CLEANING OF TOOLS
Clean all tools and equipment after use with water. Once hardened, the product can only be removed mechanically.